Why Many Warehouse Management Systems Fail and How to Avoid Common Pitfalls
- clementyou
- Jul 2, 2024
- 3 min read
Updated: Nov 13, 2024
An effective Warehouse Management System (WMS) is essential in today's dynamic business landscape to ensure a smooth supply chain and maintain a competitive edge. Despite its importance, numerous businesses struggle with WMS issues that hinder rather than improve their operations. This article will explore the main causes of WMS failures and offer guidance on selecting the appropriate system to drive your business success.
Inadequate WMS Software
One of the most common reasons for WMS failure is the use of improper software that lacks essential functionalities. When a WMS is heavily customized to meet the specific needs of a warehouse, it often leads to a myriad of bugs and system inefficiencies. This customization not only complicates the system but also makes it more prone to errors and downtime.
A robust WMS should come with a comprehensive set of features that can be tailored to different warehouse environments without extensive customization. This ensures that the system remains stable and reliable, reducing the risk of disruptions in your operations.
Outdated Software
Another significant reason for WMS failures is the use of outdated software. Many WMS lack auto-upgrade features, leaving customers stuck with old versions that become increasingly obsolete over time. An outdated WMS can lead to compatibility issues, security vulnerabilities, and reduced performance.
To avoid this pitfall, it is essential to choose a WMS that offers regular updates and upgrades. This ensures that your system stays current with the latest technological advancements, security protocols, and industry best practices, allowing your business to operate efficiently and securely.
Lack of Warehouse Domain Knowledge
The success of a WMS implementation heavily relies on the expertise of the consultants involved. Unfortunately, many WMS projects fail because the consultants lack sufficient knowledge of warehouse operations and domain-specific requirements. This lack of understanding can lead to improper system configurations, inadequate training, and ultimately, a system that does not meet the needs of the business.
When selecting a WMS provider, it is crucial to ensure that their consultants have extensive experience and knowledge in warehouse management. This expertise will help in accurately configuring the system, providing effective training, and offering valuable insights to optimize your warehouse operations.
How to Choose the Right WMS
To avoid the common pitfalls that lead to WMS failures, consider the following tips when selecting a system for your business:
Evaluate the Features: Ensure that the WMS you choose has all the necessary functionalities without requiring extensive customization. A feature-rich system will be more stable and easier to maintain.
Check for Updates: Opt for a WMS that offers regular updates and auto-upgrade features. Staying current with the latest software versions will keep your system secure and efficient.
Assess Consultant Expertise: Work with consultants who have a deep understanding of warehouse operations. Their expertise will be invaluable in configuring the system correctly and providing the necessary support and training.
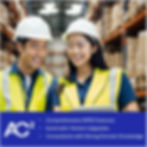
Conclusion
Choosing the right Warehouse Management System is critical for the success of your business. By avoiding systems that require heavy customization, ensuring your software stays up-to-date, and working with knowledgeable consultants, you can implement a WMS that enhances your operations and drives business growth. Stay ahead of the competition by investing in a reliable and efficient WMS that meets your warehouse's specific needs.
Ready to transform your warehouse operations? Discover how AC2 WAVE WMS can help you achieve seamless and efficient management. Learn more about AC2's WAVE WMS and take the first step towards superior business growth today!